According to history, thin films began over 5,000 years ago, however, thin film growth by sputter deposition was first reported in the early 1800s and sputter deposition was already dominating the optical coating market by 1880*.
Let’s fast forward to 1990… As a result of our successful relationship with GE, coating energy efficient IR Halogen lightbulbs with the IsoDyn® Machine for the last four years, Philips approached DSI to coat lightbulbs. The GE contract restricted DSI from using IsoDyn® for lighting products, so another coating process for lamp coating was needed.
DSI was tasked to develop a multi-layer thin film coating for Philips using magnetron sputtering. The process was developed to achieve high-rate production of multilayer metal oxide coatings on the glass envelopes of tungsten halogen lamps for energy efficiency. It utilized state-of- the art pulsed DC power supplies and a microwave generated auxiliary plasma to prevent the metal targets from poisoning and losing sputtering rate.
The process was named “MicroDyn” at a meeting called to find a name that could be used for sales and marketing. Norm Boling, one of the original founders, suggested the name. The “Micro” part came from DSI’s use of a microwave plasma that differentiated DSI’s process from others. “Dyn” comes from a unit of force, the dyne. The process was unique enough that DSI submitted a patent for their new sputtering method, only it was rejected several times before the inventor, Dr. Norm Boling, went to Washington to argue the case. DSI received the patent in 1998 for MicroDyn®.
With millions of coated bulbs required and the coating being only one step in the lamp-making process, the only cost-effective manufacturing approach was to sell Philips MicroDyn® machines with a license to coat light bulbs. Over a 15-year period, DSI sold 8 MicroDyn® machines to Philips and 3 to Osram/Sylvania.
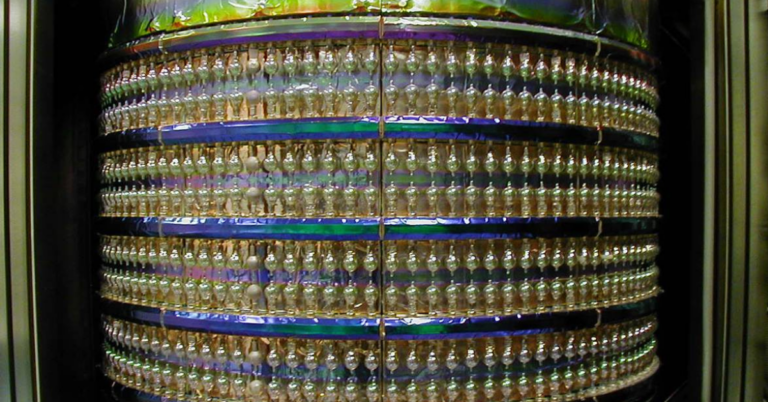
Although the process development was paid for by Philips, DSI retained the rights to use MicroDyn® to coat any product that was not a lighting component. With high deposition rates and up to 30 square feet of coated area, the process soon dominated DSI coating and has been used on hundreds of government and commercial products in the last 25 years.
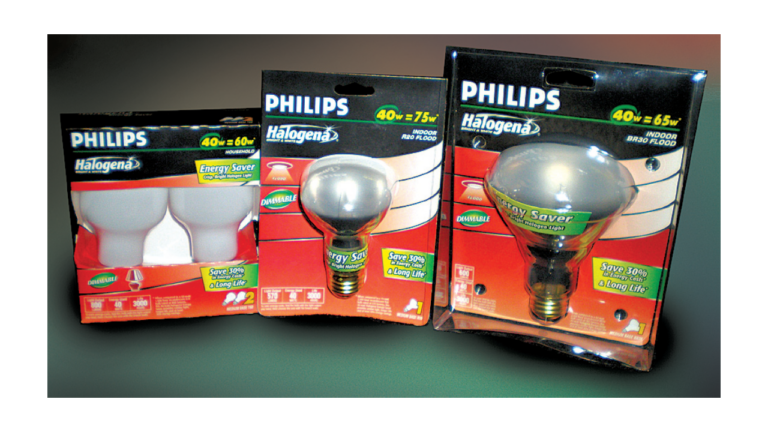
Reference:
* “Tracing the recorded history of thin film sputter deposition: From 1800’s – 2017” by J.E. Greene, article published in Journal Vacuum Science and Technology, Sept. 8, 2017.
Contact us to discuss your next custom coating project.